Sacrificial anode installation avoids structural corrosion
Client / Site: Noble Drilling, Semi-Submersible Platform, UK Continental Shelf
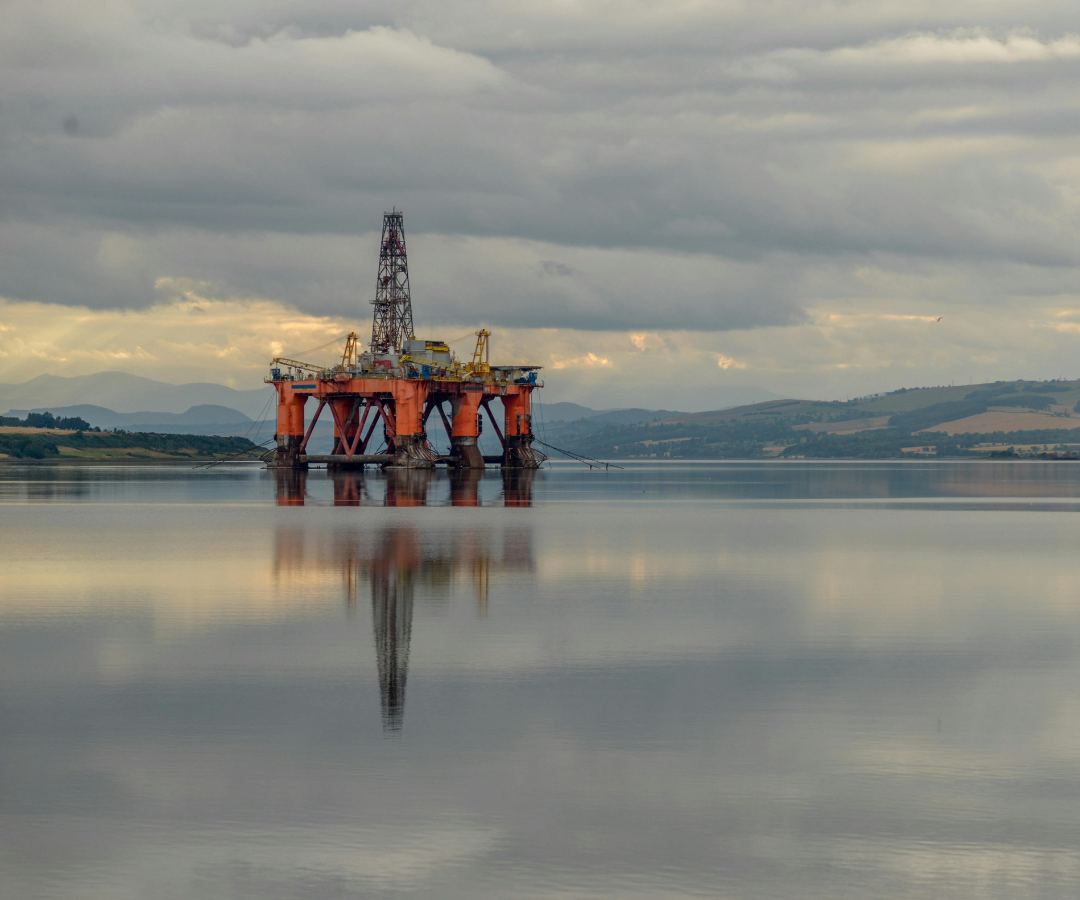
The Challenge
Noble Drilling commissioned a routine UWILD inspection for their semi-submersible rig’s ABS class renewal whilst berthed inshore. What started as standard underwater inspection quickly escalated into an emergency intervention.
During the inspection, our divers discovered catastrophic failure of the rig’s cathodic protection system – widespread depletion of sacrificial anodes across both pontoons. This represented a critical threat to the platform’s structural integrity and class certification.
The challenges became immediately apparent:
- Cathodic protection failure – Sacrificial anodes completely depleted, exposing steel structure to accelerated corrosion
- Class certification at risk – ABS surveyor witnessing live evidence of structural protection system failure
- Tight berthing schedule – Limited inshore time available for corrective action
- Scope expansion under pressure – Emergency anode replacement required alongside ongoing UWILD inspection
- No schedule flexibility – Any delays would impact operational commitments and certification deadlines
Without immediate action, the platform faced class certification failure and potential operational shutdown.
Our Response
Dagger Diving escalated the critical finding to the onboard ABS class surveyor and client engineers using live-feed verification, then rapidly expanded operations to address the situation.
Immediate Assessment – Our divers provided real-time visual documentation of the cathodic protection failure, enabling instant decision-making by ABS surveyor and Noble engineering team.
Scope Expansion – With zero delay, we mobilised additional resources for complete pontoon anode replacement whilst maintaining the original UWILD inspection schedule.
Large-Scale Replacement Programme – Our surface-supplied diving team systematically replaced 228 depleted anodes (114 per pontoon) using underwater welding capabilities and controlled installation procedures.
Dual Operations Management – We executed both emergency sacrificial anode replacement and comprehensive UWILD inspection in parallel, maximising efficiency and minimising vessel downtime.
Continuous Quality Assurance – All underwater welding and installation work was performed under fully audited Safe System of Work procedures, with live monitoring by the attending ABS class surveyor ensuring immediate compliance validation.
14-Day Intensive Operations – Our team maintained continuous operations over 14 days, working within the berthing window to complete both unexpected critical repairs and class inspection requirements.
The Outcome
Mission accomplished – class certification secured and structural integrity restored without schedule deviation.
Complete emergency response results:
- 228 sacrificial anodes successfully replaced – Full cathodic protection system restored to specification
- Full class certification retained – ABS approval achieved without delay or compliance breach
- Structural corrosion threat eliminated – Platform protected against accelerated steel deterioration
- Future drydocking avoided – Emergency intervention preventing costly mandatory repairs
- Zero project delays – Both inspection and emergency work completed within original timeline
Our rapid response and operational adaptability prevented a potential class certification crisis whilst delivering comprehensive structural protection for Noble’s critical offshore asset.
Project delivered under emergency conditions ensuring regulatory compliance and structural integrity with zero operational impact.
Performance Metrics:
- 41 successful dives completed over 14 intensive days
- Zero lost time incidents despite emergency scope expansion and underwater welding operations
- 100% class approval – Full ABS certification achieved
- Perfect safety record – No RIDDOR incidents during complex emergency operations
Technical Note: Cathodic protection systems use sacrificial anodes to prevent corrosion of steel structures underwater. When anodes become depleted, the protected steel structure becomes vulnerable to rapid corrosion. For offshore platforms, this represents a critical structural and safety risk requiring immediate intervention to maintain operational certification.